Vamos iniciar este artigo com uma parcela da história do Turbocompressor e dar sequência a muitas outras informações sobre esta máquina térmica, que faz os motores a combustão aproveitarem o máximo de energia de uma gota de combustível.
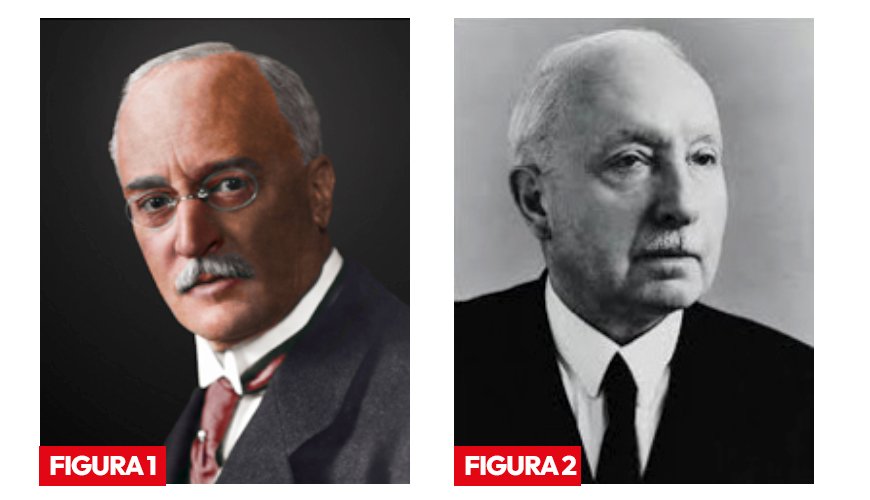
Em 1885 Gottlieb Daimler(fig.1) patenteou a ideia de, pré-comprimir o ar aos cilindros do motor, anos mais tarde isso se repetiu por Rudolf Diesel.(fig.2).
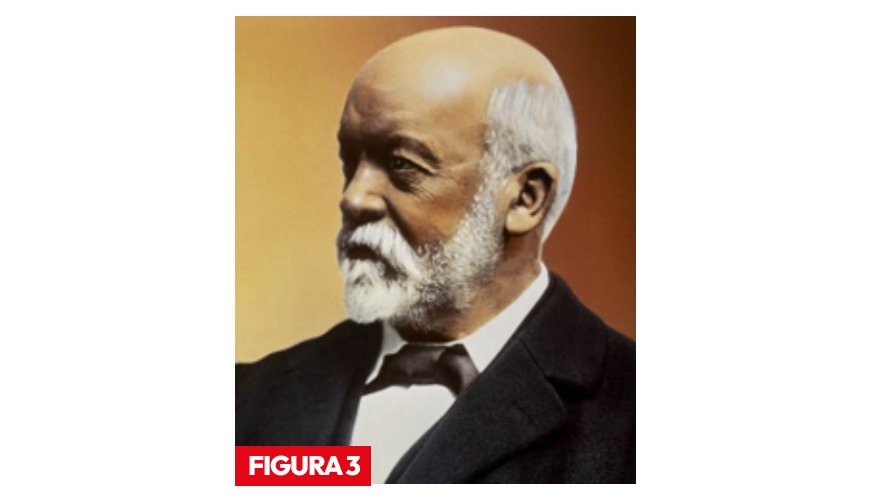
Porém o Sr. Alfred Büchi, (fig3) vinte anos mais tarde patenteou uma máquina térmica (reciprocante) que aproveitaria a energia dos gases do escape para aumentar a massa de ar absorvida pelos cilindros dos motores a combustão.
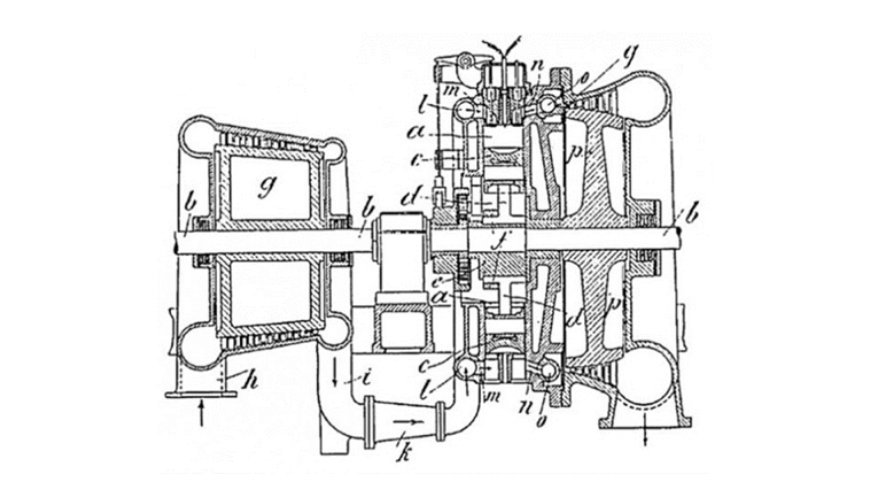
Acima, desenho do primeiro Turbocompressor, patenteado pelo Sr. Alfred na Deutsches Patent und Markenamt.
Abaixo uma propaganda sobre a aplicação do Turbocompressor nos motores de combustão interna.
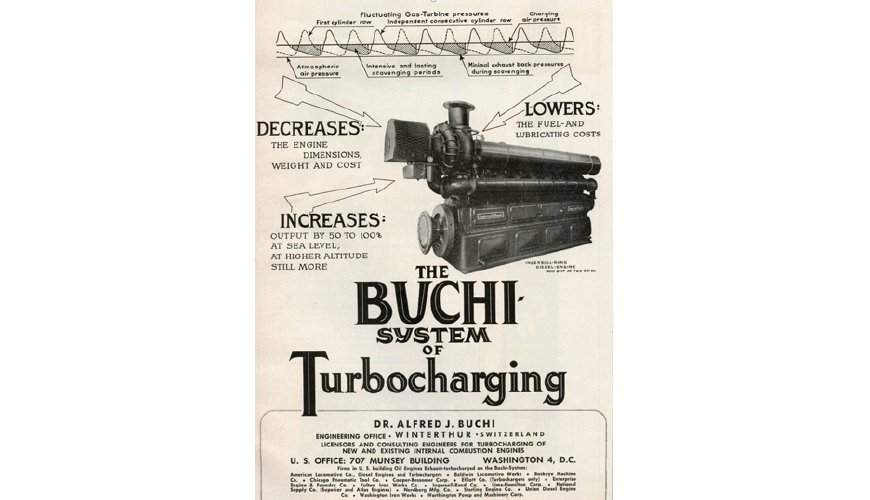
Os primeiros motores a usarem a máquina térmica do Sr. Alfred (Turbocompressor) foram as locomotivas a diesel e logo após os motores de grande deslocamento volumétrico usados na aviação, que foi o grande salto para resolver o problema da rarefação do ar (O2) em altitude, permitindo o melhor desempenho dos aviões.
O Turbocompressor é um compensador de altitude, favorece o ganho de torque, potência e torna o motor a combustão mais eficiente em todos os regimes de rotação e sendo ecologicamente correto pelo alto índice de economia de combustível e baixo nível de emissões evaporativas.
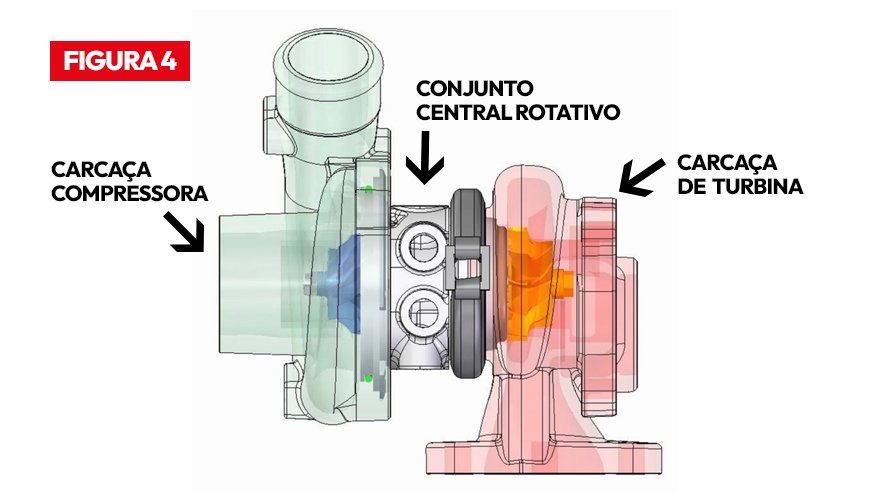
O Turbocompressor está dividido em três elementos principais: carcaça de turbina fabricada em ligas de ferro fundido e outras ligas, conjunto central rotativo fabricado em ligas de ferro fundido e carcaça compressora em alumínio. (fig.4)
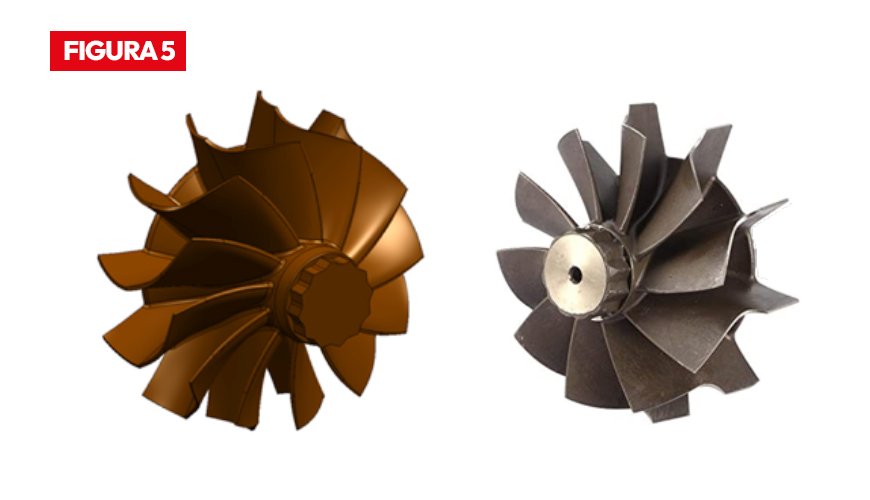
Os rotores de turbina (fig.5) são fabricados em INCONEL, superliga aeroespacial capaz de resistir temperaturas de 1050 graus, além da pressão provocada pelos dos gases do escapamento, sem apresentar deformação dos impellers (aletas), em altíssimas rotações. A turbina é o recuperador de energia.
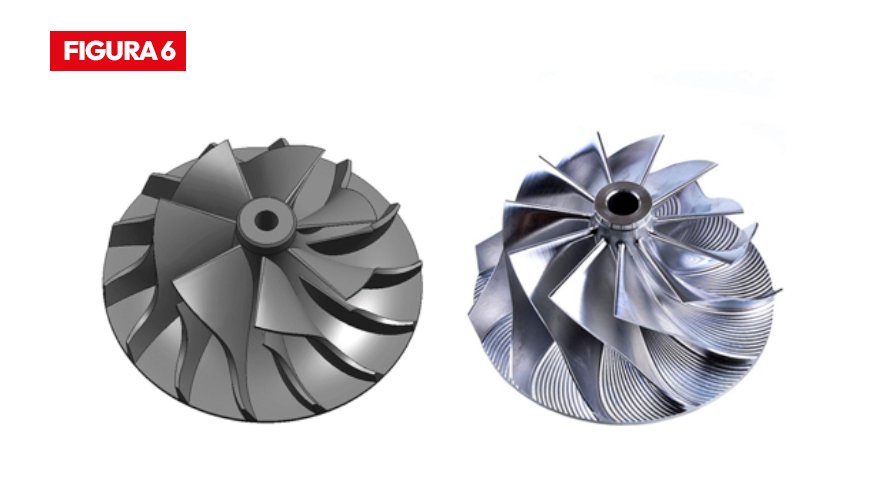
Os rotores compressores são fabricados nos seguintes materiais e processos: alumínio fundido com tratamento térmico de superfície, alumínio forjado e fresado (billet) e titânio fresado.
Atualmente o Turbocompressor pode ultrapassar os 300 mil rpm, e para tal equilíbrio harmônico entre os rotores tanto do compressor quanto da turbina é necessário realizar dois balanceamentos: individual por componente (compressor e turbina), nesta etapa é retirado material dos rotores, e o balanceamento dinâmico com a ligação do rotor compressor ao eixo rotor de turbina, montados na estrutura da carcaça central, nesta etapa é retirado material da porca de fixação do rotor do compressor.
Observação importante: essa retirada de material da porca é prevista (balanceamento dinâmico realizado em equipamentos especializados, onde todo o sistema rotativo interno da carcaça central está em movimento com rotações acima de 150 mil rpm) por tanto a porca de fixação não pode ser considerada um defeito pela retirada do material.
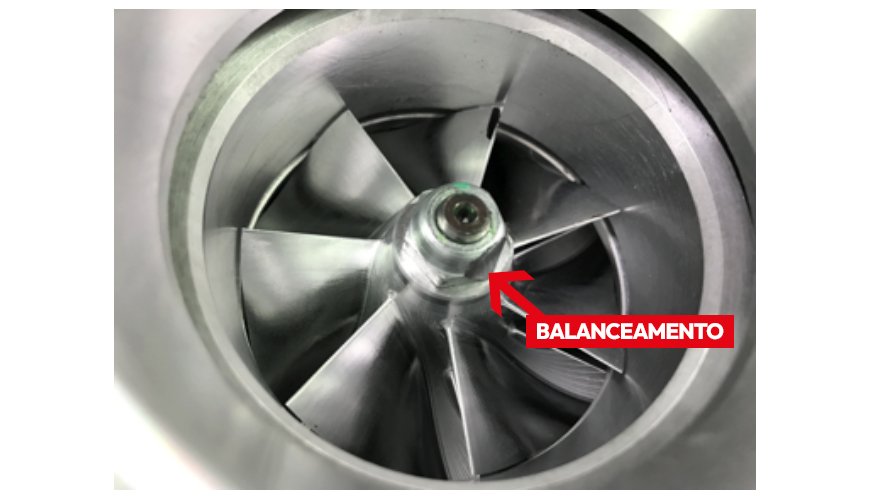
Na carcaça central o eixo é sustentado por mancal hidrodinâmico radial e ou rolamento de esferas (ballbearing).
A lubrificação do Turbocompressor é realizada pelo próprio óleo lubrificante do motor que também promove sua refrigeração, além do sistema arrefecimento que também participa por um circuito planejado no conjunto rotativo central. (fig.7)
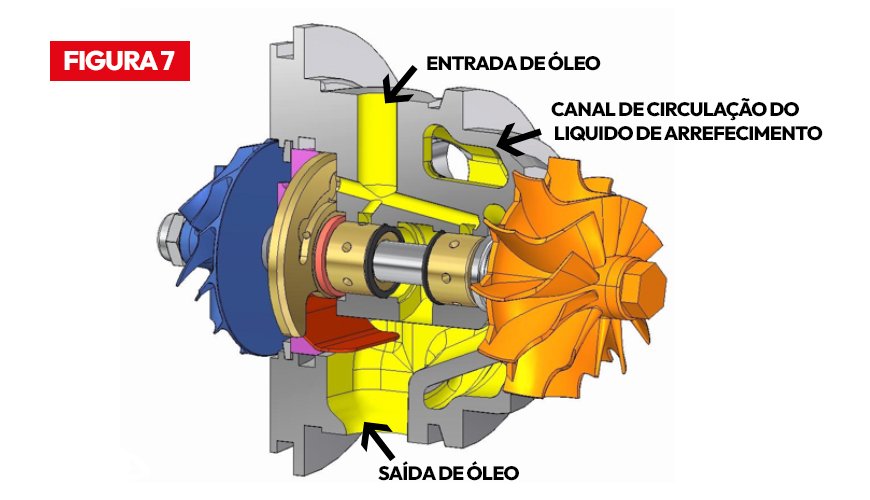
O resultado de um motor que utiliza Turbocompressor, para quem é “jovem a mais tempo” assim como eu, vai lembrar que os primeiros veículos com Turbocompressor chegaram ao Brasil na década de noventa. Vamos fazer um breve comparativo: por volta de 1993 havia um motor da Autolatina quatro cilindros de mil cilindradas com o objetivo de economia de combustível, gerando uma potência em torno de 54 CV e 7 quilos de torque com 7,78 bar de BEMP.
Hoje considerando uma trajetória de evolução de trinta anos o motor de mil cilindradas turbo alimentado gera uma potência de 128 CV e 20 quilos de torque com 21 bar de BMEP e “faltando um cilindro” perceberam o efeito Turbocompressor, repetindo, o quanto é possível de recuperar de energia de uma gota de combustível, “bem-vindo a era Turbo”!
O Turbocompressor aumentou o “folego” dos motores a combustão. Funcionamento: a carcaça da turbina conduz os gases de escape até a turbina, que por sua vez a turbina recupera energia térmica, e por efeito de expansão faz movimentar o eixo rotor que por consequência movimenta o rotor do compressor que se encontra na outra extremidade do eixo.
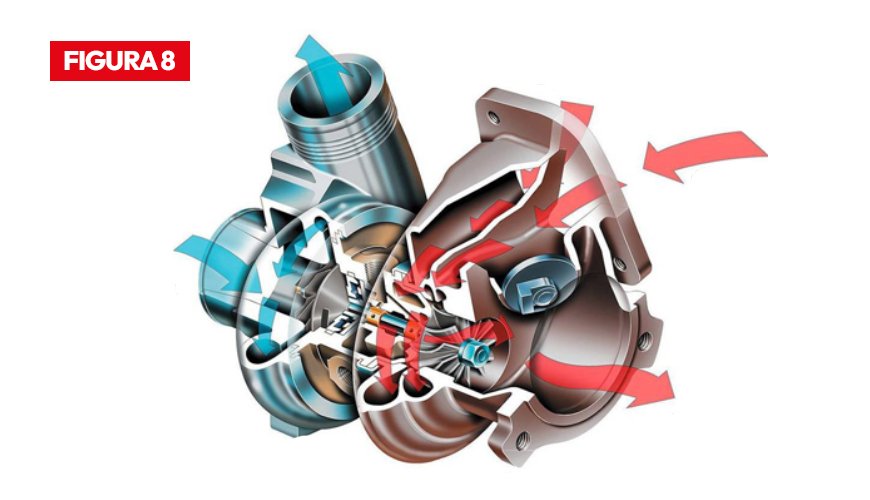
O ar filtrado é aspirado pelo rotor do compressor e comprimido na carcaça compressora seguindo em direção ao intercooler sob temperatura e pressão, após o ar ser tratado (intercooler reduz temperatura do ar) seguindo em direção ao motor sob pressão melhorando sua capacidade volumétrica.
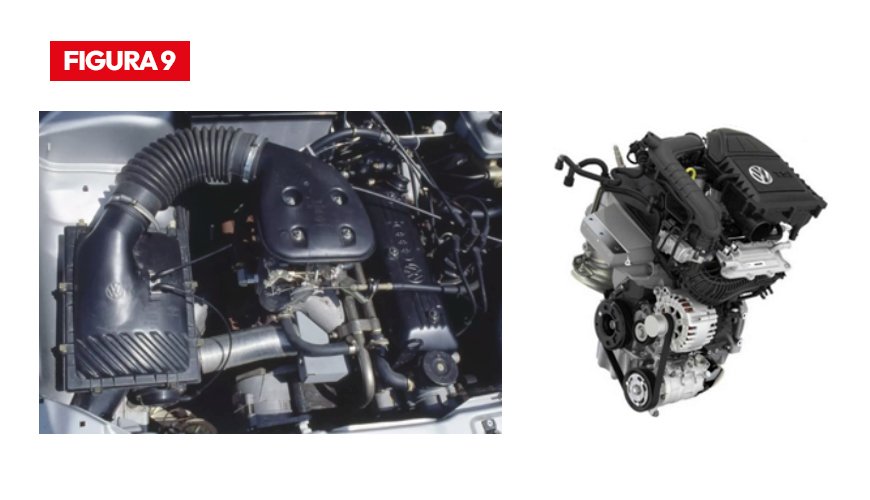
Desta maneira os motores turbos alimentados são dotados de eficiência e performance.
Até o próximo encontro turbinado!

Marcio Cattani, tem atuação na área técnica automotiva desde 13 anos. Consultor Técnico MasterPower Turbo, atendendo o mercado brasileiro e Internacional, suporte ao pós venda, engenharia de desenvolvimento, suporte técnico e treinamento técnico. Instrutor Homologado Bosch em Diagnóstico Eletrônico. Foi instrutor de treinamento fábrica MWM motores para rede Servico MWM. Com Especialização em Sistemas Eletrônicos Embarcados e Veículos Híbrido pela Universidade de Ávila Espanha.
marciocattani.mc@gmail.com / Siga no Instagram: @marciocattani
Baixe os catálogos dos fabricantes apoiadores da Revista Reparação Automotiva
Acesse a banca digital da Revista Reparação Automotiva
Inscreva-se no Canal TV Reparação Automotiva no Youtube
Siga a Revista Reparação Automotiva no Linked In
Siga a Revista Reparação Automotiva no Instagram