Sistema de injeção direta de combustível
Conheça todos os componentes e a maneira correta de realizar o diagnóstico com scanner e manômetro no Sistema de injeção direta de combustível
As normas de preservação do meio ambiente, como por exemplo, a limitação da quantidade de gases tóxicos que podem ser emitidos nos escapamentos dos automóveis são cada vez mais rígidas. Para atender estas normas a engenharia das fabricantes de veículos trabalham com seus fornecedores, no caso os sistemistas, para desenvolver soluções que deixem os carros menos poluentes.
Entre estas soluções encontradas está o sistema de injeção direta de combustível, o qual vem sendo adotado nos motores. No sistema de injeção convencional o combustível é injetado no coletor de admissão, enquanto que, na injeção direta, ele acontece na câmara de combustão. Sendo assim, a queima é mais eficiente, o que gera menor consumo e consequentemente menos emissões.
Paulo Stevanato, instrutor técnico CTA Bosch, explica que o sistema de injeção indireta é mais simples e com menos componentes. “Ele possui uma bomba que leva o combustível sob determinada pressão até a peça conhecida por flauta, porém a nomenclatura correta é rampa de distribuição, onde há uma pressão fixa que injeta o combustível”. No entanto, a injeção direta é mais complexa e tem componentes semelhantes aos utilizados na injeção indireta. “A injeção direta de combustível é composta por dois sistemas de alimentação de combustível, um de baixa pressão e outro de alta pressão. Ele é semelhante ao diesel common rail”, complementa o instrutor. Apesar de ser um sistema complexo, o reparador atento não encontra dificuldades ao realizar diagnósticos ou reparos, desde que tenha o conhecimento técnico, como é mostrado nesta reportagem realizada no CTA-Centro de Treinamento Automotivo Bosch, localizado em Campinas (SP)
Assista ao vídeo desta matéria técnica no Youtube TV Reparação Automotiva
Componentes do sistema de injeção direta de combustível
Na linha de baixa pressão há uma bomba de combustível, a qual na maioria dos casos não é uma bomba tradicional, o módulo alimenta a bomba e ela gera vazão constante de combustível. O sistema de injeção direta possui um conjunto chamado DECOS (Demand Control System– sistema de controle de demanda), o qual está dentro do tanque e entrega a quantidade de combustível necessária para o motor funcionar.
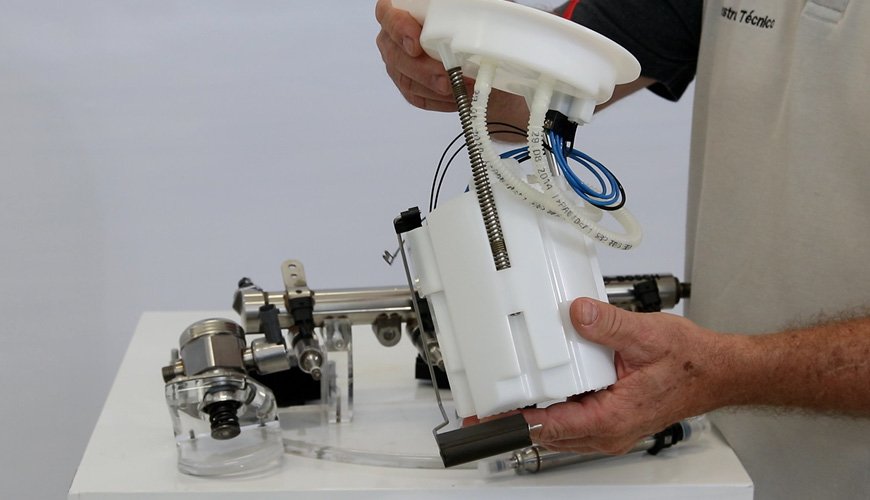
O módulo de controle recebe a solicitação de pressão e volume de combustível a ser injetado.
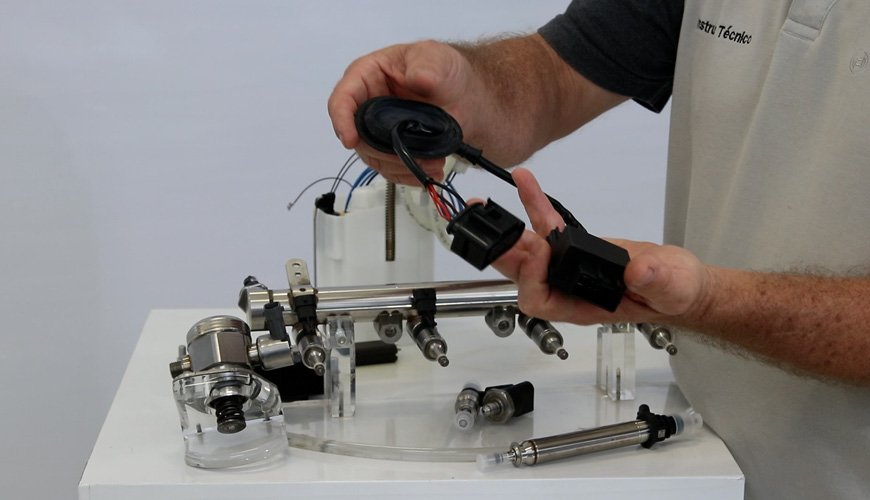
O módulo de gerenciamento do motor analisa todas as variáveis de funcionamento e envia um sinal para determinar a elevação da pressão de injeção do combustível. Depois disso o módulo da bomba atua na bomba elétrica para que ocorra a vazão correta de combustível no Rail ou rampa de injeção alimentar do motor.
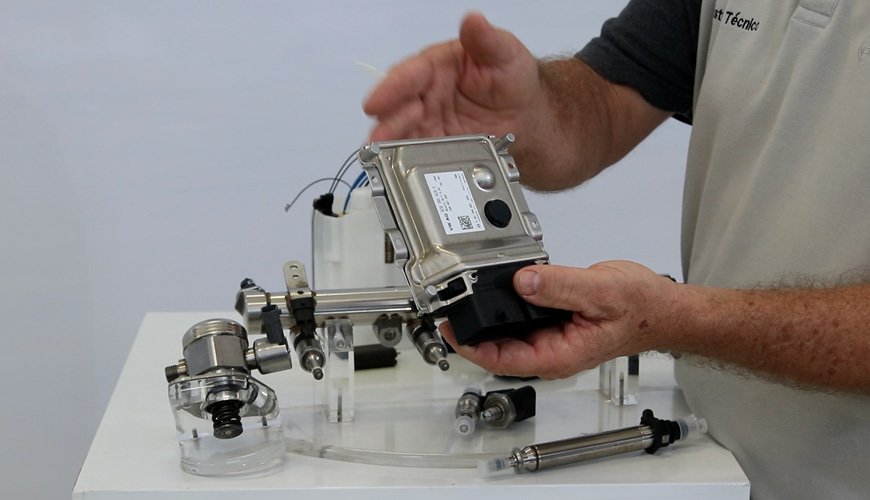
Enquanto que no sistema de injeção indireta a flauta é plástica, no sistema de injeção direta a rampa de injeção, flauta ou tubo, é metálica. Este material é utilizado para suportar a alta pressão de trabalho, pois em determinados veículos essa pressão pode chegar até 350 bar.
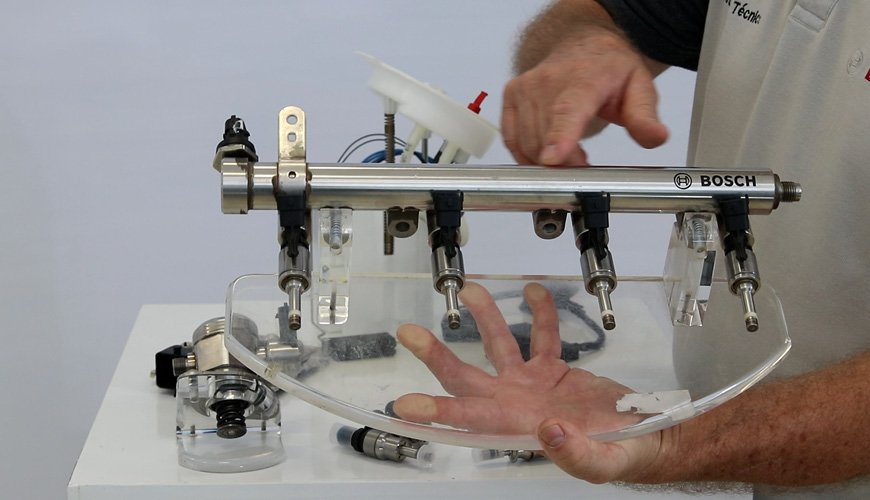
Localizado na extremidade da rampa de injeção, o sensor de pressão transforma uma grandeza física em elétrica. Este sinal é enviado para a ECU do motor a qual faz a leitura e determina se há necessidade de aumentar ou diminuir a pressão para o regime do motor.
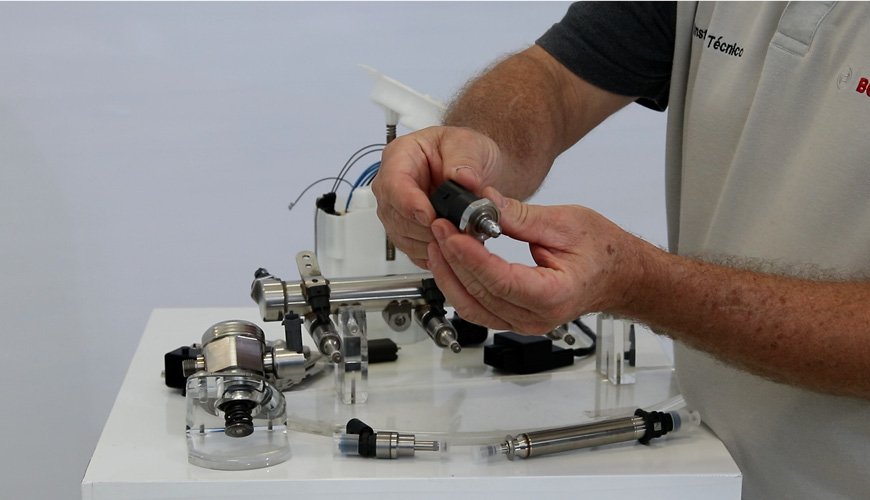
No Rail há os injetores de combustível, um dos tipos de injetor é o bobinado, o qual é semelhante ao injetor da injeção indireta.
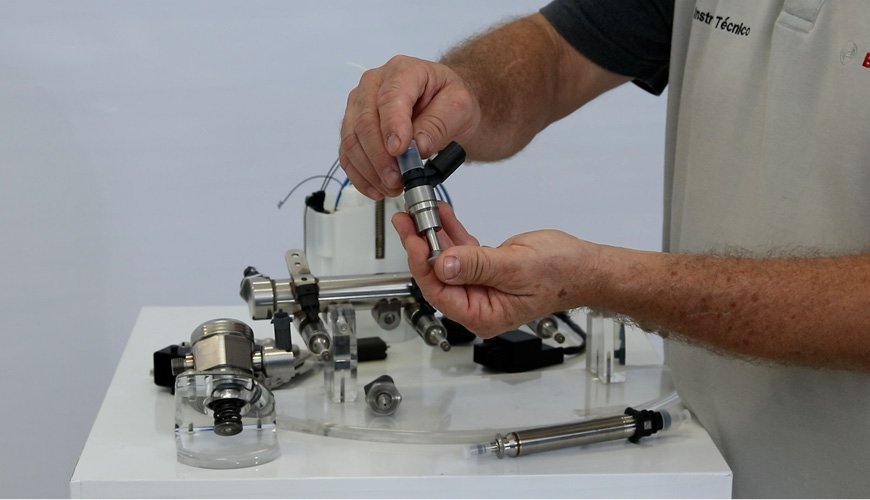
O outro tipo de injetor é o piezoelétrico, ele possui tecnologia mais avançada. As dimensões e características são diferentes dos bobinados. Um deles tem a dimensão maior para acomodar a bobina e o outro é totalmente cilíndrico. A escolha do tipo de injetor está condicionada as leis de emissões exigidas pelo país que o veículo é fabricado. Há casos que é necessário mais de uma injeção por ciclo, exigência que o injetor bobinado não atende. Já o injetor piezoelétrico trabalha em velocidade de abertura e fechamento mais alta e atende estas exigências.
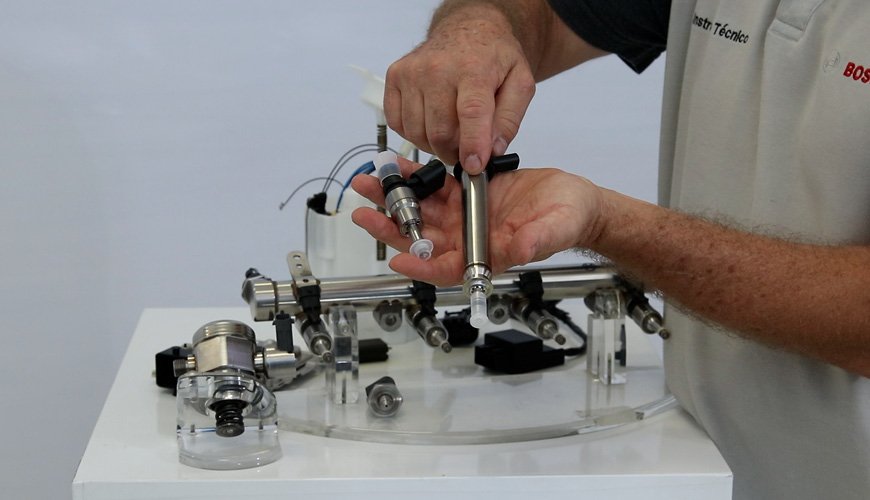
A bomba de alta pressão possui uma entrada e uma saída de combustível. Sendo assim, a bomba de baixa envia o combustível com uma pressão que varia entre 3 a 7 bar para a bomba de alta, que pode ser chamada de coração do sistema. A bomba de alta recebe o combustível e envia com pressão de até 350 bar. Estes valores de pressão não são padrão, pois eles variam de acordo com as exigências das normas de emissões do país que o veículo é comercializado.
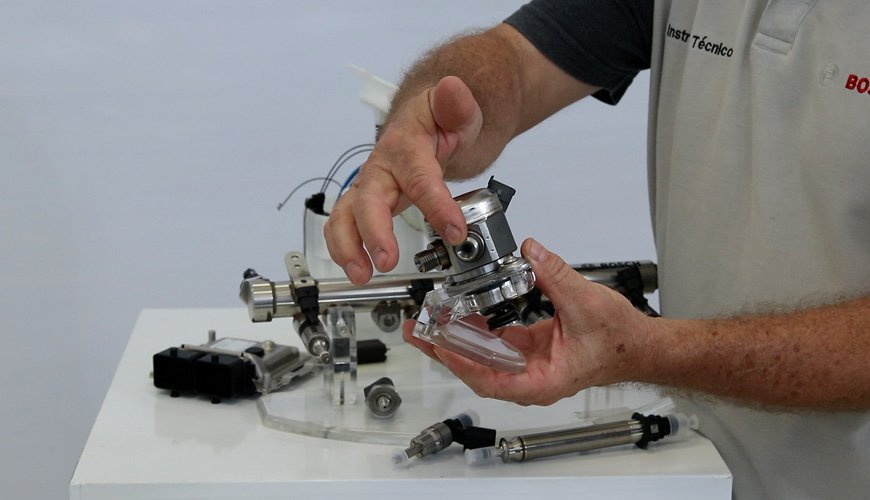
Através de uma frequencia o sensor de etanol identifica a quantidade e a temperatura do etanol no tanque. Se a temperatura estiver baixa ele eleva a pressão para ter uma melhor atomização do combustível. Isso forma gotículas que são mais fáceis de queimar e não prejudica a partida com temperaturas baixas. Este sensor adota regimes de controle de pressão e injeção diferentes, de acordo com a necessidade.
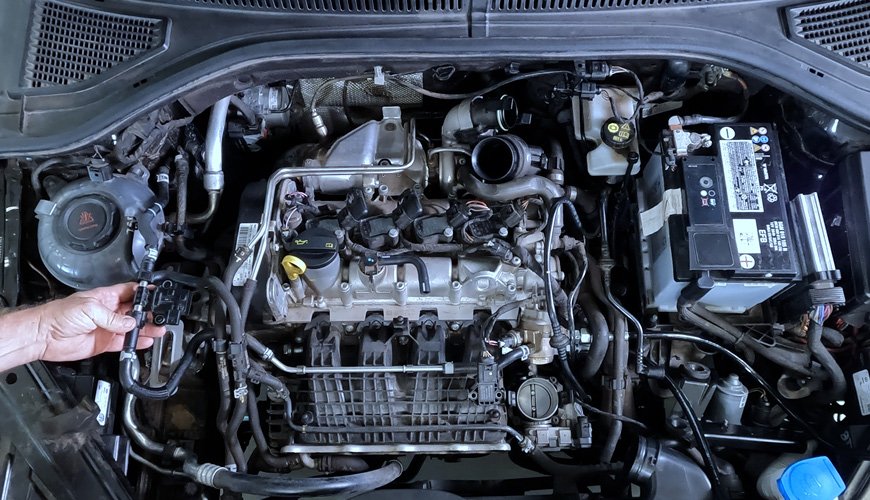
Diagnóstico da injeção direta de combustível
Iniciar o diagnóstico no tanque de combustível, fazer primeiro a medição da pressão na bomba de baixa, pois ela envia a quantidade de combustível para o Rail. Esta medição pode ser feita a partir do tanque ou no compartimento do motor.
1. Instalar manômetro na linha de baixa e equipamento de diagnóstico, o scanner, na porta OBD
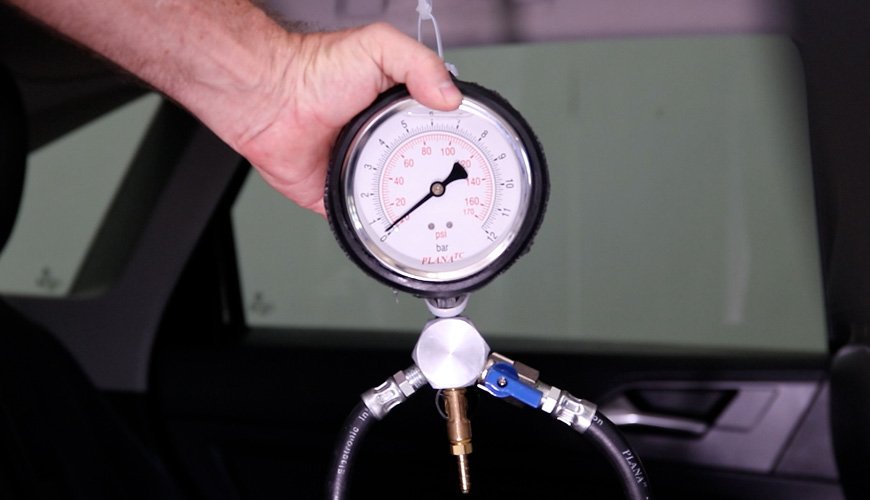
2. Acionar o comando do scanner para iniciar a bomba de baixa
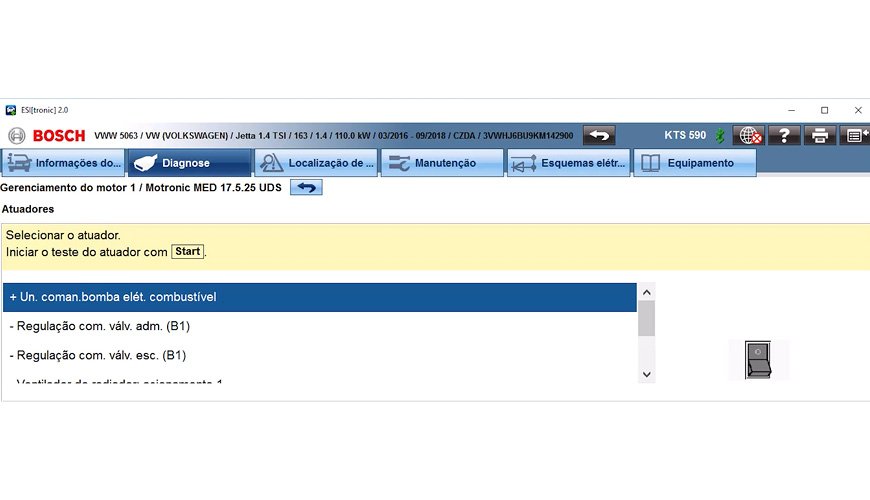
3. Verificar a pressão indicada no manômetro. Ela deve estabilizar próximo aos 7 bar, neste caso chegou a 6,5 bar, a pressão de trabalho está correta
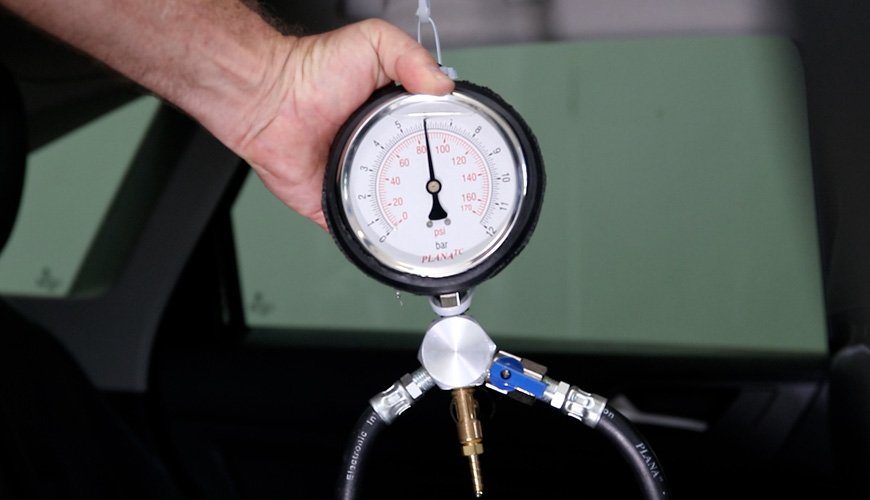
4. Desligar a bomba no scanner. Ao verificar o manômetro a pressão deve se manter, caso ela caia muito rápido é sinal de que há problemas na bomba de baixa
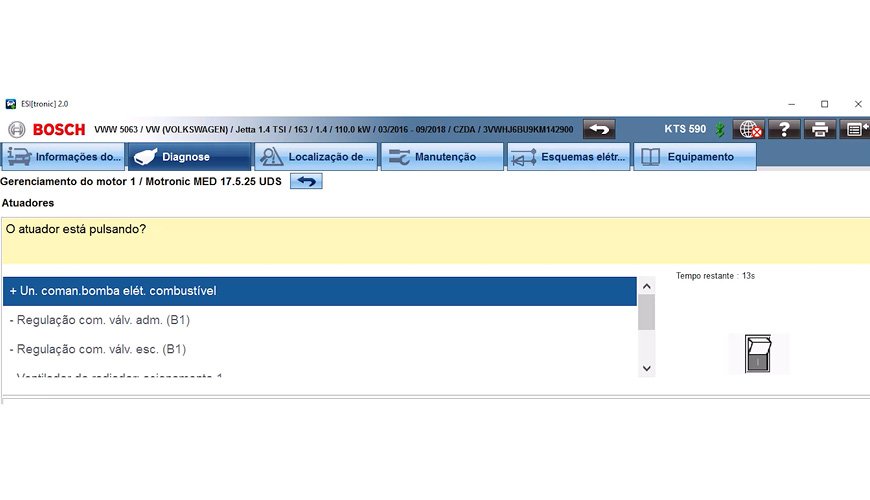
Diagnóstico na linha de alta pressão
5. Fazer a leitura da pressão na linha de alta no scanner. Para isso, dar a partida no motor, ele irá mostrar o valor real da pressão, ela gira em torno de 125 a 130 bar, a temperatura e o tipo de combustível, no caso o Etanol. Esta última leitura é feita através do sensor de combustível. Ao ligar o motor ele está frio, depois de aquecido, a pressão estabiliza-se em torno de 110 bar. Para saber o máximo de pressão atingida, basta acelerar até o final do curso do acelerador, quando a pressão chegará a 190 bar, isso porque o veículo está parado. A carga máxima de 350 bar só irá ser atingida com o veículo em movimento, por isso, para saber a pressão total do sistema o teste deve ser feito também com o carro em movimento
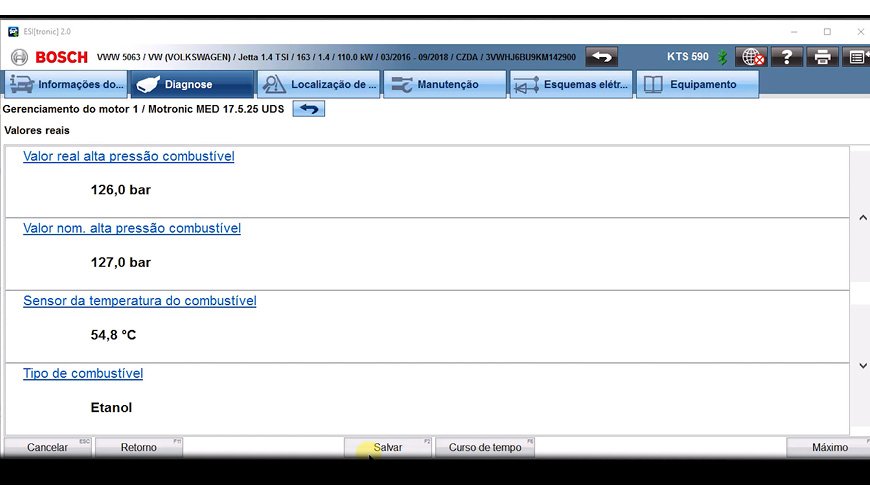
6. Para confirmar que a pressão está correta fazer também a leitura com o manômetro de alta pressão. Ele deve ser instalado entre o Rail e a bomba de alta pressão.
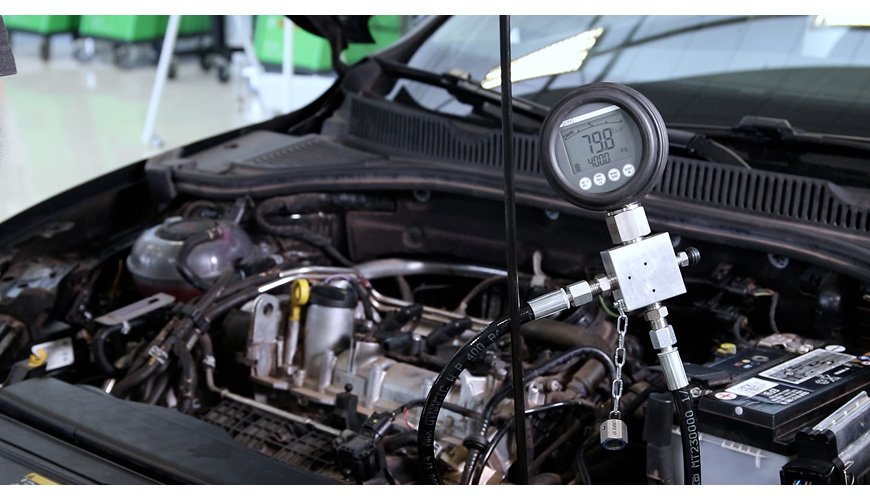
7. Fazer a análise de estanqueidade da bomba, para isso desligar o motor e manter a ignição ligada. Verificar no scanner a pressão mostrada. Ao desligar o motor a pressão estava em 82 bar e chegou a 86 bar. Isso ocorre porque há combustível na linha e após desligar o motor ele expande e aumenta a pressão. O scanner mostra o valor real da pressão, o informado pelo sensor ao módulo, e o valor nominal é da programação especifica do módulo. Caso haja uma diferença grande entre a pressão real e a nominal todo o sistema deve ser checado e analisado, pois ele pode estar comprometido
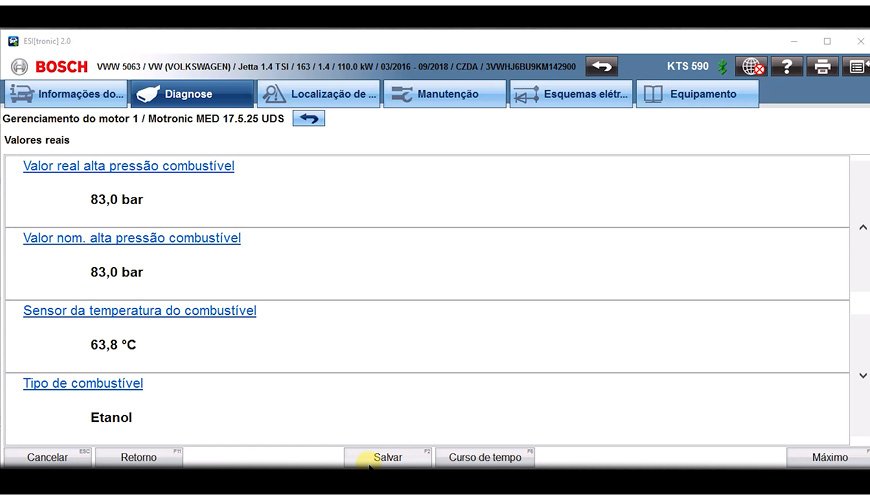
Obs: A análise de estanqueidade da bomba de alta também pode ser feita por gráficos, para isso, basta desmarcar as opções: tipo temperatura e tipo de combustível e selecionar esta opção no scanner.
Injeção direta com sistemas eletrônicos e mecânicos
A bomba de alta pressão é acionada pelo comando de válvulas, ou seja, o contato é mecânico, conhecido na oficina como o ‘contato ferro com ferro’, por isso, para preservar o sistema e manter o funcionamento de maneira correta é necessário seguir rigorosamente o período recomendado para a troca do óleo do motor e utilizar o lubrificante específico indicado pela fabricante do veículo. Ao utilizar o lubrificante errado pode ocorrer desgaste entre o ressalto do comando ou tucho de acionamento da bomba, assim ela não atingirá a pressão de trabalho. Por isso, no caso de diferença acentuada entre a pressão real e nominal, além do diagnóstico na linha elétrica, também é necessário verificar a parte mecânica. Para isso remover a bomba, verificar se há desgaste, verificar se a mola do embolo não está quebrada.
Também é necessário ficar atento a qualidade do combustível, pois o combustível adulterado irá gerar carbonização na ponta do injetor que está na câmara de combustão e no momento da injeção, provoca dispersão do jato de combustível, perca da homogeneização da mistura e consequentemente alteração nas emissões. A sonda lambda irá gerar código de falha, mistura pobre, ou mistura rica, ou fora do especificado.
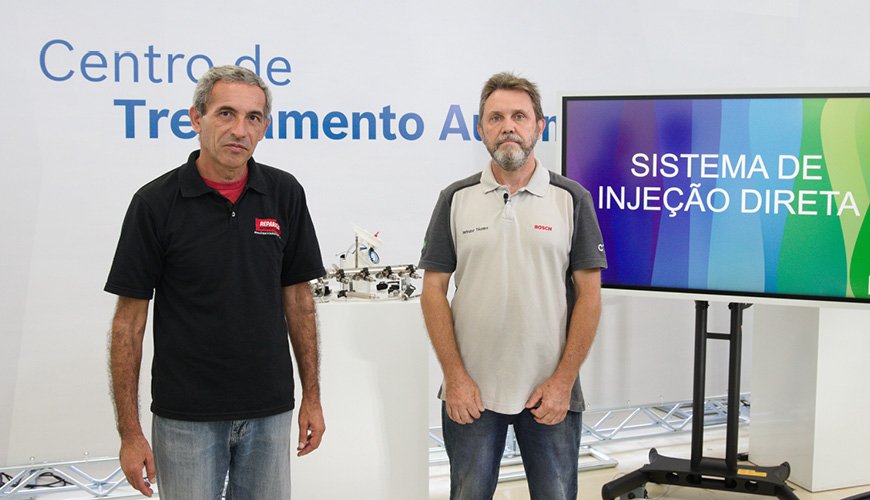
Mais informações: CTA Bosch – Fone: 0800 7045 4446 – www.bosch.com.br
Baixe os catálogos dos fabricantes apoiadores da Revista Reparação Automotiva
Ouça o Podcast da Revista Reparação Automotiva
Acesse a banca digital da Revista Reparação Automotiva
Inscreva-se no Canal TV Reparação Automotiva no Youtube
Siga a Revista Reparação Automotiva no Linked In
Siga a Revista Reparação Automotiva no Instagram