Sensores de velocidade e rotação, eles são complicados? Utilizam somente dois ou três fios? Sendo assim, o que há para aprender? Bem, imagine inspecionar um sensor de velocidade de roda com um osciloscópio e ver o padrão de sinal da figura 1, enquanto a roda está girando. Imagine então sua surpresa quando você souber que o padrão está perfeitamente correto. A primeira parte deste artigo discute como funcionam os sensores de rotação básicos, que são utilizados na indústria automotiva por vários anos, e na segunda parte introduz os sensores de rotação avançados encontrados em muitos veículos modernos.
Estes sensores de rotação avançados hoje são utilizados para medir giro de virabrequins, eixos comando de válvulas, rodas, e rotação de eixos de transmissão em transmissões comuns, tais como a 8L90, 10L/R80, ZF9HP48, para citar apenas algumas. Antes de falarmos desses sensores de alta tecnologia, vamos voltar ao passado e ver como eles evoluíram.
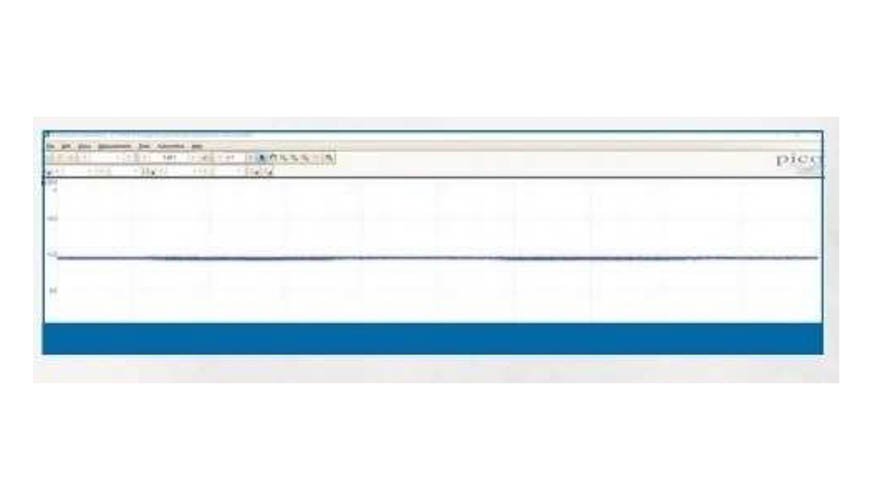
SENSOR DE ROTAÇÃO PASSIVO RELUTÂNCIA VARIÁVEL (VR)
Quando consideramos um sensor de rotação, podemos visualizar um simples sensor de dois fios que gera uma forma de onda senoidal, de tensão alternada, conforme visto na parte final da figura 2. Estes sensores, chamados de relutância variável (VR), tem servido a indústria por décadas, e são comumente usados para medir rotações de simplesmente qualquer componente. Tal como um virabrequim, eixo comando de válvulas, vários eixos de transmissões, rotação de rodas, e basicamente tudo que gira em um veículo. A construção de um sensor VR é muito simples. Ele é composto de um ímã permanente enrolado em uma pequena bobina de fios finos.
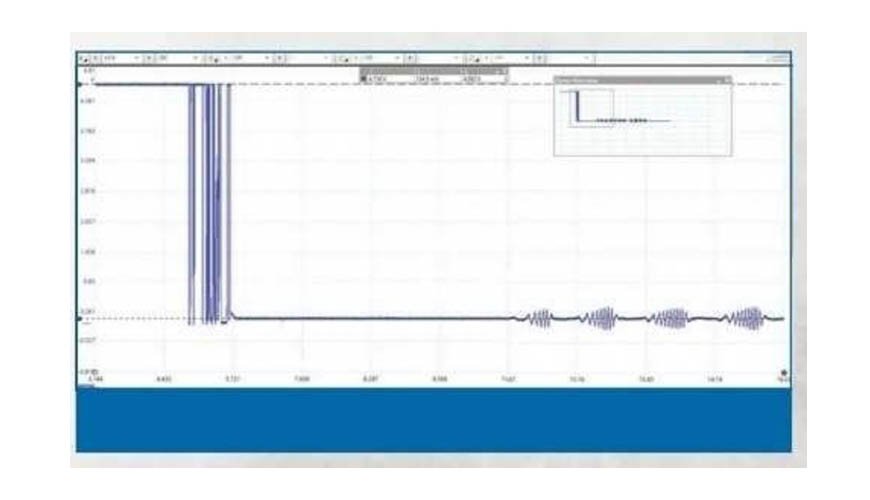
Ele opera sob os princípios da “indução” – onde um campo magnético induz corrente em um fio ou condutor. Com o sensor de rotação VR, quando um ímã está próximo à uma roda de impulsos dentada metálica, suas linhas de fluxo se concentram ou retraem em direção aos dentes metálicos. E quando a roda de impulsos gira um pouco, um espaço de ar se abre ao redor do ímã, e então as linhas de fluxo se expandem para fora. Esta expansão e contração destas linhas de fluxo invisíveis faz com que uma tensão e corrente sejam induzidas na bobina. Um computador pode contar estes pulsos, interpretar os resultados, e determinar a velocidade de giro. Não podemos imaginar algo mais simples do que isto.
Agora, na eletrônica automotiva, para finalidade de diagnóstico, deve existir uma tensão na saída do circuito do sensor de rotação VR em direção ao módulo de comando, conforme mostra a figura 3.
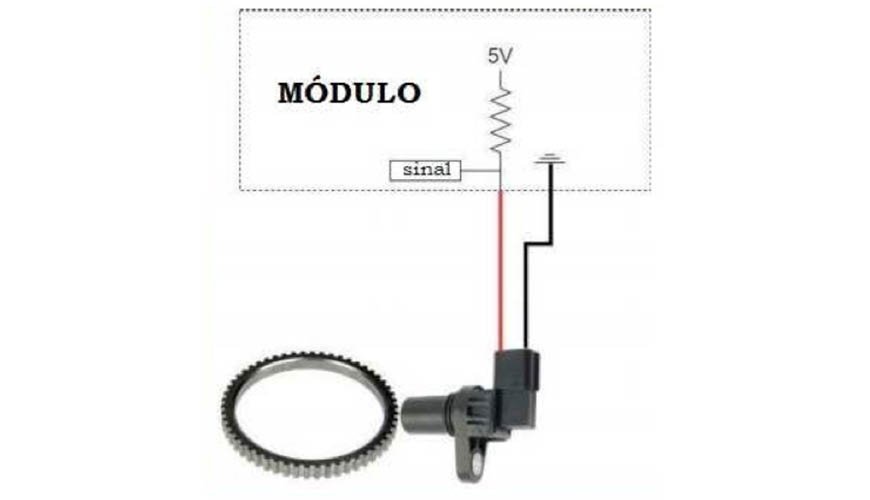
Contudo, o sensor não é alimentado de nenhuma maneira. O módulo existe para determinar se o circuito do sensor está aberto ou fechado. Se testarmos o circuito enquanto o sensor está desligado, podemos encontrar 5V nos fios do circuito. Com o sensor conectado, podemos encontrar 0,5V ou menos através do circuito, porque agora o sensor compartilha aquela tensão com uma resistência localizada no módulo.
Se o computador (módulo) detectar 0V (curto circuito) ou 5V (circuito aberto), nos fios do circuito do sensor, ele sabe que existe um problema e relatará um código de falha apropriado para o problema. A figura 2 mostra o sinal de velocidade da roda de um ACURA MDX 2007, e mostra a tensão de um circuito aberto a 4,7 Volts, uma tensão de circuito fechado de 135 mV, e o padrão de uma onda senoidal de 433 mV AC, mostrada no topo daquele 135 mV DC.
O ponto fraco dos sensores VR (relutância variável) mostrados na figura 4, é que ele perde a força do sinal quando o RPM baixa, eles são sensíveis à interferências elétricas externas. A perda da força do sinal é decorrente das linhas de fluxo magnético que se expandem e se contraem, através da bobina do sensor pela indução AC. As linhas de fluxo não se expandem e contraem rápido o bastante através da bobina do sensor para gerar uma tensão significativa. Ele também não é tão preciso com um sensor digital. Se a posição, precisão e sensibilidade às baixas RPM são necessárias, os fabricantes poderão optar por um sensor do tipo magneto-resistivo ou um sensor de efeito Hall.
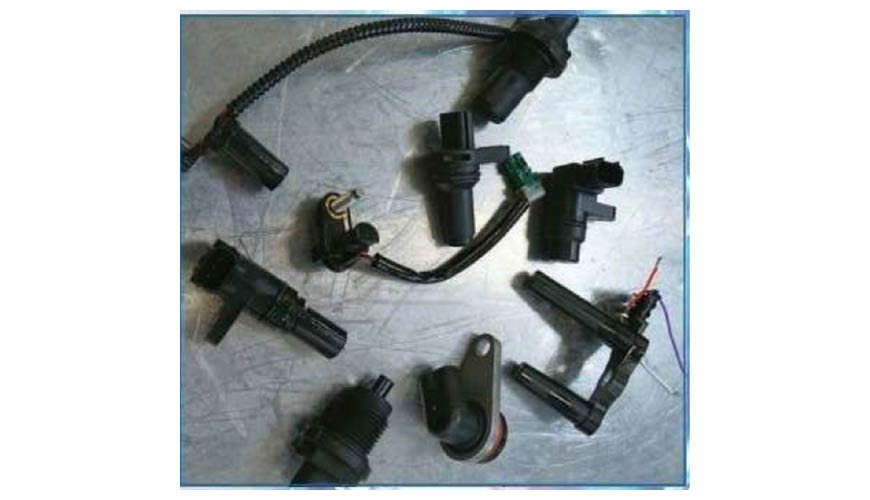
O sensor VR também é muito suscetível à interferência eletromagnética (EMI) de fontes externas, tais como sistema de ignição, alternador, solenoides, relés e injetores. Os dois fios do sensor VR são frequentemente torcidos ou blindados por uma malha metálica para repelir quaisquer interferências que possam ser induzidas em seus fios.
Práticas comuns de diagnóstico incluem verificar a resistência da bobina do sensor com o auxílio de um multímetro, medindo a tensão gerada pelo sensor quando se esfrega uma massa metálica nele, e utilizando um osciloscópio para verificar a qualidade de seu sinal. Muitos técnicos optam por substituir o sensor quando desconfiam dele, porque estes sensores são relativamente baratos, e a compra de um novo frequentemente pode ter uma relação custo benefício muito boa, do que perder tempo diagnosticando o mesmo. Se o sensor for muito caro ou não estiver facilmente disponível no mercado para compra, a execução de testes básicos poderá confirmar se ele está OK ou não.
Utilizando um Ohmímetro para verificar a resistência do sensor VR é o teste mais simples. Veja as informações de serviço quanto às especificações de resistência do sensor sob teste nos manuais. Os valores de resistência variam desde 500 Ohms em uma transmissão 41TE até 2.400 Ohms em uma transmissão Allison ou maiores ainda. Se a informação não estiver facilmente disponível na literatura técnica da transmissão, siga as orientações normais de diagnóstico para teste do sensor, mesmo que não haja DTCs listados no sistema.
Se o teste de resistência passar, teste quanto à saída de tensão alternada com o multímetro e monitore a tensão pico a pico. Seria bom ter outro sensor sabidamente em bom estado para comparar os resultados do teste. O valor típico de uma tensão pico a pico deve ser forte o bastante para que o computador aceite este sinal gerado. O computador não continuará contando pulsos se a tensão cair a valores muito baixos. A força do sinal AC pode variar grandemente entre aplicações. O sinal de uma roda por exemplo na figura 2 é menor que 0,5V AC quando se gira a roda com as mãos, enquanto que o sinal de velocidade em um Trail Blazer 2006 (Figura 5) está ao redor de 5V Ac quando se gira o eixo cardã com as mãos. Apenas tenha em mente que a amplitude do sinal (força) vale muito quando os sensores são de relutância variável (VR).
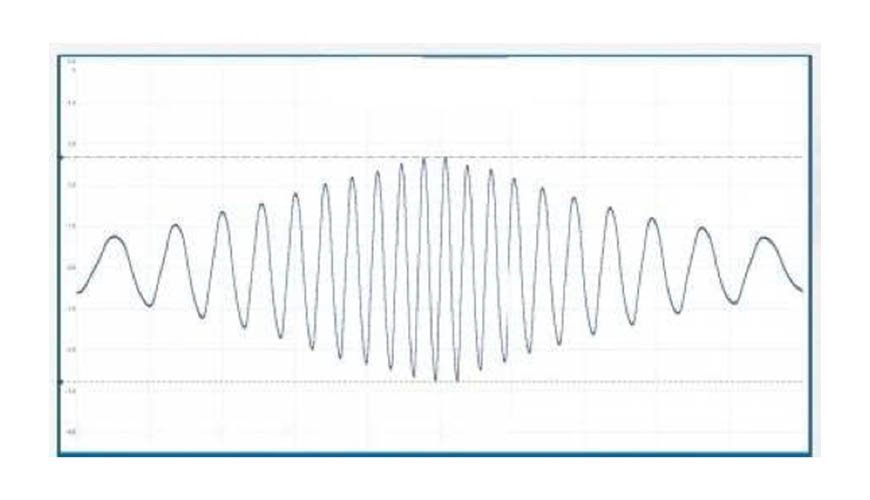
Um osciloscópio poderá fornecer o inteiro quadro quando se faz o diagnóstico de um sensor de rotação VR. Entre os benefícios de se utilizar um osciloscópio é o de poder ver a qualidade dos padrões, bem como a tensão. Se existir uma roda fônica danificada, por exemplo, ou um dente amassado, ou se a tensão de saída do sensor flutuar excessivamente, tudo isto pode ser visualizado com o auxílio de um osciloscópio. Em conclusão, o sensor VR é muito confiável e trabalha nos veículos por vários anos, ainda é encontrado em numerosas aplicações, embora seja mais difícil de ser utilizado nos veículos mais modernos. Muitos agora são sensores de rotação “ativos” que emitem um sinal digital. O sinal digital é eficiente nas baixas rotações e determina com bastante precisão posições de eixos, a quaisquer rotações.
SENSORES DE ROTAÇÃO ATIVOS DE EFEITO HALL E MAGNETO- RESISTIVOS
Um sensor de efeito Hall tipicamente possui três fios: Uma alimentação positiva (5V, 8V, 9V ou mesmo 10V são comuns). O sensor de efeito Hall ainda utiliza a influência de um ímã, mas utiliza o campo magnético para disparar o sensor e inserir uma tensão na fiação do circuito, gerando um padrão de onda quadrada DC que o computador pode usar para determinar posição e velocidade ou rotação. A figura 6 mostra o sinal de dois sensores de rotação do eixo comando de válvulas de um Cadillac CT5. O sensor de efeito Hall de três fios é muito utilizado para se medir a rotação e ponto dos motores, e é também encontrado em muitas transmissões. Existem poucas maneiras de se avaliar este sensor eletricamente.
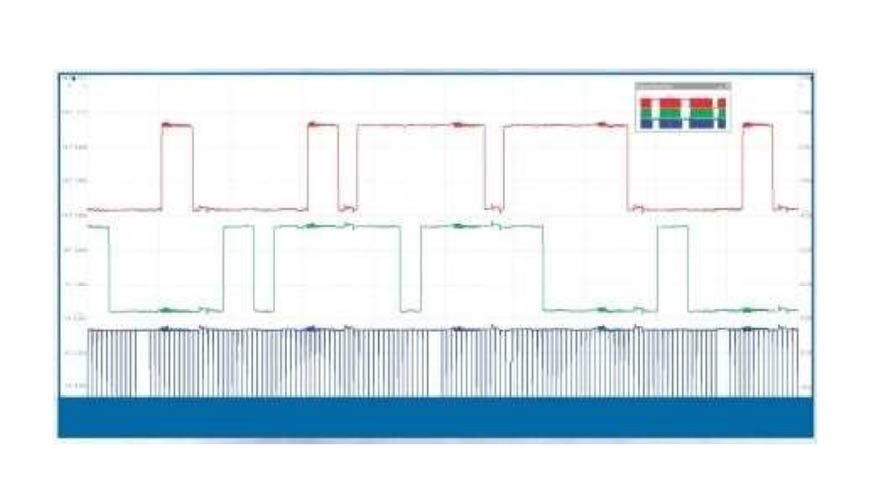
Com o auxílio de um multímetro digital, podemos constatar se existe tensão de alimentação no circuito do sensor e uma queda excessiva de tensão ou voltagem no circuito de aterramento. Podemos também medir a tensão do fio de sinal e girar lentamente o componente para se certificar que a tensão varia de próxima a zero até a tensão de alimentação do circuito, qualquer que seja ela. Por exemplo, na figura 7, o sensor do Nissan Sentra, que é alimentado com uma tensão de 5 V, varia de 5V de sinal até 0V de sinal. Este veículo trabalha corretamente, mas pelo fato de o sensor não levar o sinal próximo a zero poderia levantar algumas bandeiras se o veículo tivesse algum problema. O 0,5V neste Nissan é devido ao fato de que existe uma queda de tensão no circuito de aterramento do sensor, o que é um pouco excessivo.
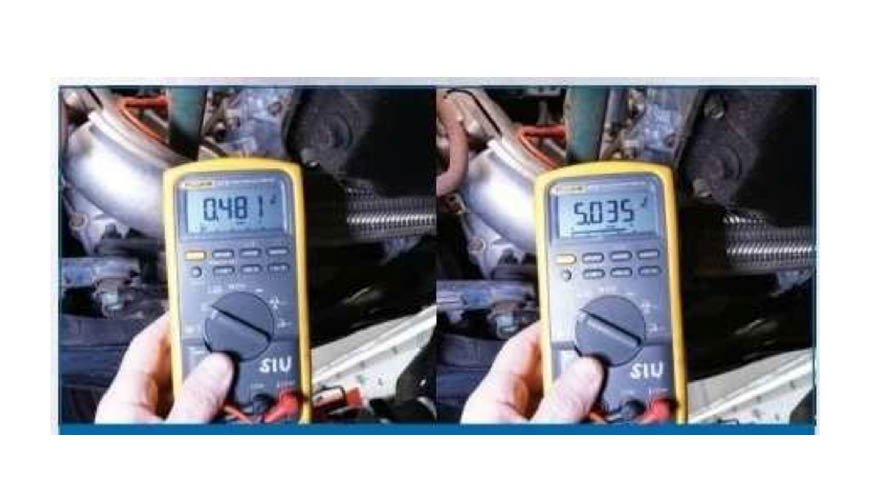
Para verificar falhas intermitentes, aplique um pouco de calor com um soprador térmico, e talvez também algumas batidas suaves no corpo do sensor, para verificar se a tensão é cortada no circuito dos fios do sensor. Devido à rápida interrupção e da natureza do multímetro, não podemos avaliar efetivamente um sensor de efeito Hall com um Multimetro Digital quando o motor ou a transmissão está funcionando. Também, não espere testar este tipo de sensor com um ohmimetro devido ao fato de os circuitos integrados internos possuírem uma resistência muito alta, e os resultados não levarão a uma conclusão confiável. Podemos testar o desempenho do funcionamento de um sensor de efeito Hall utilizando um osciloscópio. Observando a figura 6, nos sinais dos eixos comandos de válvula, podemos ver uma tensão liga/desliga que cai próxima de zero (0,1V) e sobe até 5V. Um osciloscópio executa um grande trabalho mostrando ruídos e sinais erráticos, mas não se esqueça de confirmar os níveis de tensão. Se o timing do componente for essencial, um osciloscópio também permite que você compare múltiplos sinais de sensores. O sensor de efeito Hall é muito confiável e robusto e pode medir com bastante precisão rotação a qualquer velocidade, mas é comum também encontrar sensores magneto resistivos em lugar de um sensor de efeito Hall quando as condições de operações do sensor podem ser um pouco duras.
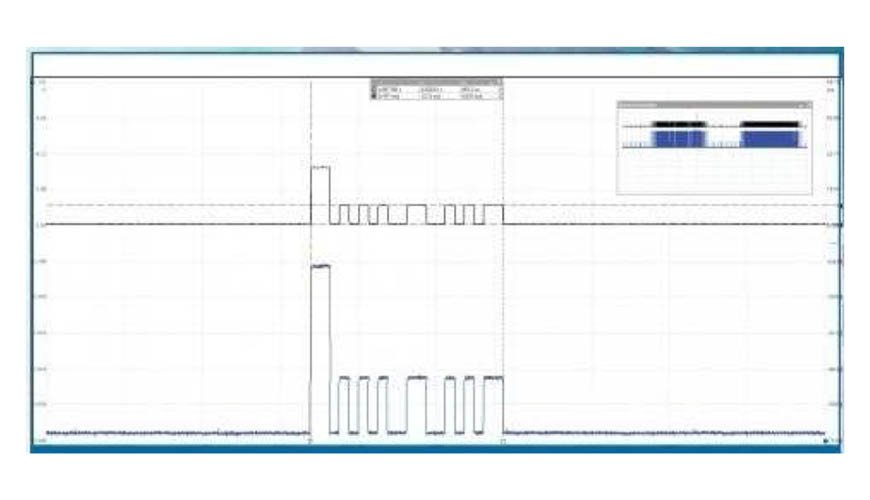
Para concluir esta primeira parte, os sensores de relutância variável (VR) e de efeito Hall tem executado uma ampla gama de trabalhos em motores, transmissões, e sistemas de controle de estabilidade em todos estes anos. O sensor VR não é mais tão comum hoje em dia, mas o de efeito Hall é ainda largamente utilizado em veículos modernos. Na segunda parte deste artigo, mostraremos alguns avanços nos sensores de rotação que melhoram a precisão, determinam o sentido de rotação, e oferecem mesmo um “pouquinho” de autodiagnóstico. Como uma pequena amostra e spoiler, a figura 8 mostra o padrão de um pulso simples de um sensor de rotação de roda moderno. Na próxima edição, iremos explorar estes sensores avançados.
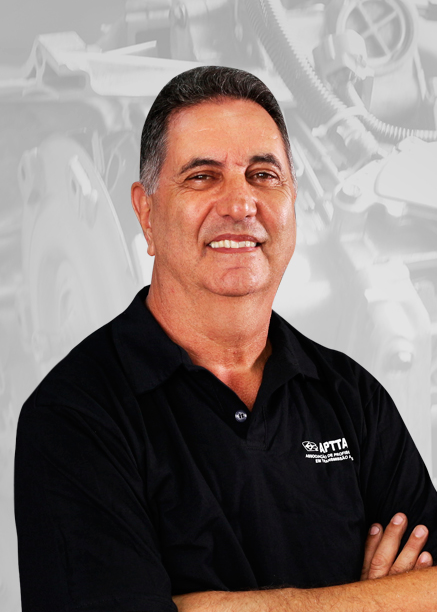
Receba todas as notícias da Revista Reparação Automotiva no seu WhatsApp
Leia os artigos dos Especialistas da Reparação
Acesse a banca digital da Revista Reparação Automotiva
Inscreva-se no Canal TV Reparação Automotiva no Youtube
Assista ao Podcast da Revista Reparação Automotiva
Baixe os catálogos dos fabricantes apoiadores da Revista Reparação Automotiva
Siga a Revista Reparação Automotiva no Linked In
Siga a Revista Reparação Automotiva no Instagram
Siga a Revista Reparação Automotiva no Facebook
Leia o conteúdo técnico da Revista Reparação Automotiva
Veja mais notícias do mercado automotivo
Leia nossa seção sobre veículos híbridos e elétricos